Riduci gli sprechi di materia prima e taglia i costi con lo stampaggio a iniezione multiugello
Il settore dello stampaggio a iniezione è in continua evoluzione, offrendo soluzioni sempre più innovative per migliorare la qualità del pezzo stampato e ridurre i costi nella produzione di O-Ring e articoli tecnici in gomma. Tra le opzioni disponibili, spiccano due approcci principali: lo stampaggio a iniezione tradizionale con un unico ugello e la tecnologia multiugelli. In questo articolo esploreremo entrambe le opzioni per aiutarti a fare la scelta migliore per le tue esigenze di produzione.
La tecnologia tradizionale di stampaggio a iniezione utilizza un unico ugello per l’iniezione della gomma o del silicone. Tuttavia, questa metodologia può comportare sprechi di materiale dovuti alla formazione di maggiore sfrido durante il processo di iniezione.
D’altro canto, la tecnologia multiugelli implica un maggiore investimento iniziale perché utilizza un blocco termoregolato a canali freddi montato sui piani della pressa. Questa attrezzatura separa il flusso di materiale in ingresso, distribuendolo ai vari ugelli (4/8/12/16).
Se l’investimento iniziale è maggiore, come e quando questa tecnologia mi permette di risparmiare?
Semplice: gli ugelli iniettano direttamente il materiale nella cavità, riducendo la lunghezza dei canali di distribuzione. Questo implica una notevole riduzione di sfrido, che nello stampaggio di grandi lotti con mescole costose si traduce in un enorme risparmio continuo.
Per comprendere meglio i vantaggi della tecnologia multiugelli, prendiamo in considerazione uno studio di caso pratico.
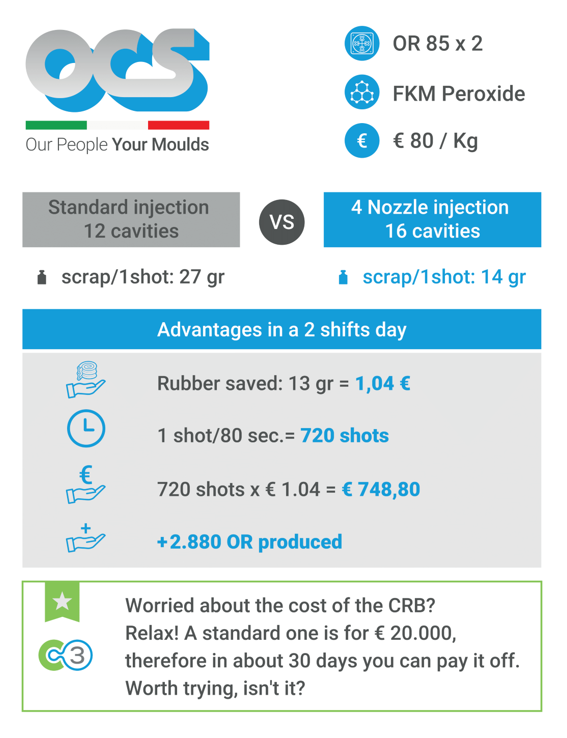
Immaginiamo la produzione di O-Ring con il materiale FKM Peroxide, noto per il suo costo elevato.
Con uno stampo di iniezione standard dotato di un solo ugello centrale e 12 cavità, lo scarto di materiale per ogni ciclo di stampaggio è di 27 grammi. Se utilizzassimo uno stampo a iniezione dotato di quattro ugelli lo sfrido si ridurrebbe a 14 grammi per ciclo.
La differenza può sembrare piccola, ma ha un impatto significativo in termini di risparmio.
Ipotizzando 80 secondi per ciclo e quindi 720 cicli al giorno su due turni di lavoro, il risparmio giornaliero ammonterebbe a circa 750 euro, oltre alla produzione di 2880 pezzi in più rispetto a quanto sarebbe possibile con uno stampo tradizionale.
Sei interessato a scoprire come puoi ridurre gli sprechi di gomma e diminuire drasticamente i costi di produzione?
Il nostro team tecnico è a disposizione per fornirti supporto e training personalizzati presso la tua azienda. Per prenotare un incontro con noi, contattaci all’indirizzo info@ocs-stampi.it.