Reduce raw material waste and cut costs with multi-nozzle injection moulding
The injection moulding sector is constantly evolving, offering increasingly innovative solutions to improve the quality of the moulded articles and reduce costs in the production of O-Rings and technical rubber articles. Among the available options, two main approaches stand out: traditional injection moulding with a single nozzle and multi-nozzle technology. In this article, we’ll explore both options to help you make the best choice for your manufacturing needs.
Traditional injection moulding technology uses a single nozzle for injection of the rubber or silicone. However, this methodology may result in waste of material during the injection process
On the other hand, multi-nozzle technology implies a higher initial investment because it uses a thermoregulated cold runner block mounted on the press. This equipment separates the flow of incoming material, distributing it to the various nozzles (4/8/12/16).
If the initial investment is greater, how and when does this technology allow me to save money?
Simple: the nozzles directly inject the material into the cavity, reducing the length of the distribution channels. This implies a considerable reduction of waste, which in the moulding of large batches with expensive compounds translates into enormous continuous savings.
To better understand the benefits of multi-nozzle technology, let’s consider a practical case study.
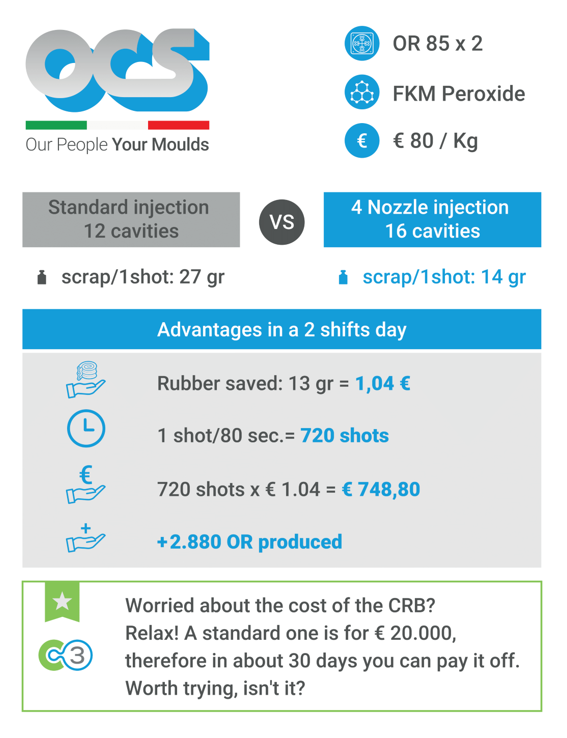
Imagine the production of O-Rings with the material FKM Peroxide, known for its high cost.
With a standard injection mould with only one central nozzle and 12 cavities, the material waste for each moulding cycle is 27 grams. If we used an injection mould equipped with four nozzles, the material waste would be reduced to 14 grams per cycle.
The difference may seem small, but it has a significant impact in terms of savings.
Assuming 80 seconds per cycle and therefore 720 cycles per day on two shifts, the daily savings would amount to about 750 euros, in addition to the production of 2880 pieces more than would be possible with a traditional mould.
Are you interested in finding out how you can reduce rubber waste and drastically reduce production costs?
Watch our video training Maintenance Guidelines for yOur Moulds. We have created a video course with practical and effective tips which help to lengthen the mould life cycle and facilitate the moulding process. Click here to watch it now:
https://www.ocs-stampi.it/en/maintenance-guidelines-for-your-moulds/